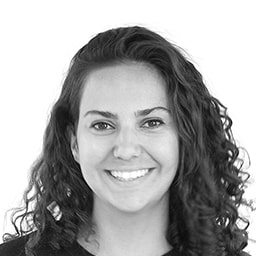
Hélène Pilkiewicz — October 06, 2017
What do your calculator and a garden chair have in common?
Have you ever wondered how the electronic devices you’re surrounded with are made? We’ve already published the 3D models and the source code of our calculator, but we thought it would be great to also share our whole manufacturing process.
Mass production of a device requires a huge number of steps. Let’s start from the top!
Injection molding
From disposable knives to garden chairs, most plastic products are injection molded. This is a widespread process because it allows complex parts to be manufactured at a high rate and for a reasonable unit price. Our calculator is no exception.
Injection molding is a simple concept: a mold is filled with molten plastic. Once the plastic cools down and solidifies, we can retrieve the plastic part. Sounds easy, doesn’t it? In practice, it’s a bit more complicated.
A simple example
Let’s take the bottom part of our calculator as an example, as it is the simplest part of the device.
Suppose the mold is in a single block, we fill its cavity with liquid plastic from an opening. But how do we retrieve the part once it has solidified?
Sure, we could break the mold apart, but that would mean manufacturing a whole new mold for every single part. That would be incredibly expensive because molds are made out of extremely strong alloy to withstand molten plastic. Anyway, it would be way too tedious to create the mold cavity from a tiny opening.
The solution is actually simple: build a mold in two parts. Just like a waffle iron!
Ejecting the part
Once the part has cooled down, we open the mold to retrieve it. Plastic always shrinks when it cools down, so the part always sticks to the innermost mold half. To detach the part from the mold, we drill holes into the mold and slide in metal rods that poke the part out. The rods are called ejector pins.
To optimize the production speed, the part is ejected from the mold before it has fully cooled down. It’s still a bit soft, and when the ejector pins jab the part out, they leave a mark on it.
Those ejector pin marks are visible on many plastic products like disposable knives or garden chairs. On products made of several parts, like our calculator, the marks are hidden on the inside. This way, they’re invisible on the assembled product!
Once the part has been ejected from the mold, an operator retrieves it and checks it for defects. It’s then ready for the rest of the assembly process!
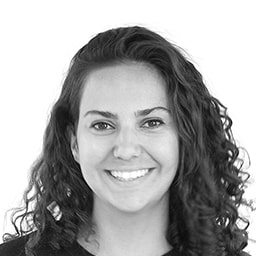
Hélène Pilkiewicz — Industrial Engineer
Hélène is the creator of all the physical aspects of the NumWorks graphing calculator. She joined our team in September 2016 as an Industrial Engineer. Hélène has a Master's in Industrial Engineering. She works on everything involved with producing the calculator: design of plastic parts, choice of suppliers and monitoring of production and quality. Every time you use your calculator, you are touching Hélène's masterpiece! When not tinkering in her workshop, Hélène is finding new and interesting ways to eat her favorite food: broccoli!